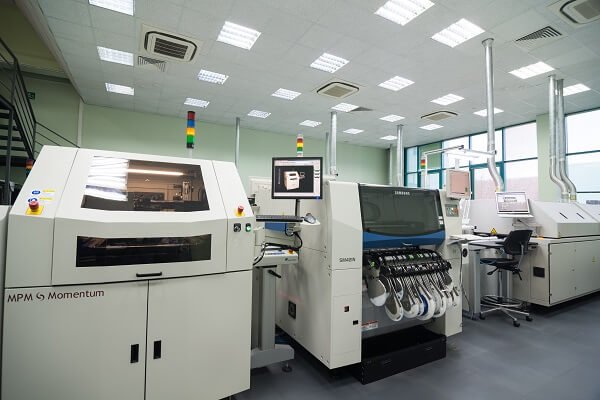
Wave Soldering Oven: Benefits, Technology, and Best Practices
Surface Mounted Devices (SMDs) are ubiquitous in electronics manufacturing, but not all SMT assembly processes are created equal. While reflow soldering is by far the most common method, sometimes SMDs on a board, such as chip components, must be wave soldered. This is particularly true when passive components are mounted on the bottom side of a PCB and held in place by dots of adhesive. While reflow oven passes can be used for top-side SMDs, wave soldering is often the preferred method for these particular assemblies.
What is wave soldering?
Wave soldering is a technique used in PCB assembly that allows through-hole components to be soldered onto the board. It is called "wave" soldering because a wave of molten solder passes over the PCB, thus bonding the components to the board. This technique is used in conjunction with SMT and is particularly effective for components that are difficult or impossible to place using SMT equipment, such as connectors or other large components.
Why use a wave soldering oven?
There are several benefits of using a wave soldering oven for PCB assembly:
1. Cost-effective: Wave soldering equipment is less expensive than reflow soldering equipment, and requires less maintenance.
2. High-volume production: Wave soldering can process large volumes of boards at one time, making it ideal for manufacturers with high production demands.
3. Reliable: Wave soldering provides consistent and reliable joint quality, ensuring the long-term reliability of the board.
4. Minimal board damage: Wave soldering equipment holds the board firmly in place during the soldering process, minimizing the potential for board damage.
How does wave soldering work?
Wave soldering equipment uses a conveyor belt to move the board through the machine. The board is first cleaned and fluxed before it is preheated to a temperature that will activate the flux. The board is then passed over a wave of molten solder, which attaches the through-hole components to the board. The board is removed from the wave soldering oven and allowed to cool, after which time it can be inspected and tested.
Best practices for wave soldering
1. Design considerations: When designing a board for wave soldering, it is important to consider the placement of the through-hole components. These components should be located on the top side of the board to avoid damage during the wave soldering process.
2. Flux application: Proper flux application is critical to the success of the soldering process. Flux must be applied in sufficient quantity to ensure a good bond between the component and the board.
3. Solder temperature: The temperature of the wave must be carefully controlled to ensure that the solder joints are formed properly. If the temperature is too high, the solder may overheat and damage the board.
4. Preheat profiles: The preheat profile is critical to the success of the wave soldering process. The board must be preheated to a temperature that will activate the flux, but not so high that it damages the board.
The bottom line
Wave soldering is a reliable and cost-effective method of soldering through-hole components onto a PCB. It is particularly effective for passive components mounted on the bottom side of a board. By following best practices for flux application, temperature control, and preheat profiles, manufacturers can ensure consistent and reliable joint quality. If you're looking for a high-volume production solution that offers minimal board damage and long-term reliability, wave soldering may be just what you need.