In the world of electronics manufacturing, PCB assembly is a critical process that requires precision and attention to detail. One of the most important aspects of PCB assembly is soldering, which involves joining components to the board through the use of solder. There are various methods of soldering, including wave soldering, which is a popular choice for through-hole components.
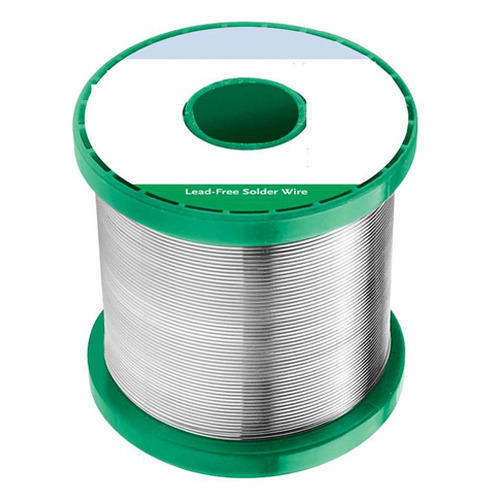
However, as with any process, PCB assembly and wave soldering can come with their own set of challenges. In this blog, we'll discuss some of the challenges that arise during PCB assembly with through-hole components and how to overcome them using a wave soldering machine.
Challenge #1: Short pins on through-hole components
As mentioned in the introduction, short pins on through-hole components can be a significant challenge during wave soldering. In some cases, the pins on the components may not be long enough to penetrate all the way through the board, making it impossible to solder them from the bottom side.
Solution: Replace components with longer pins
One solution to this issue involves replacing the components with longer pins. However, this can be a labor-intensive process, as the original pins need to be manually removed, and longer pins need to be inserted. Once this is done, the components can be reinserted, and wave soldered from the bottom side.
Challenge #2: Mixed assembly with surface mount components
Mixed technology assembly involving surface mount components and through-hole components can also be a challenge. The surface mount components can become damaged during the wave soldering process, making it necessary to protect them during the soldering process.
Solution: Use a solder mask
One solution to this issue is to use a solder mask. A solder mask is a protective barrier that prevents the solder from coming into contact with the surface mount components. This can be especially useful during wave soldering, as the solder tends to flow over the entire board and can end up on the surface mount components. With a solder mask in place, this is prevented, ensuring that all components are safe during the soldering process.
Challenge #3: Proper cleaning of the board
After wave soldering, it's important to clean the board to ensure that no residual flux or other contaminants remain on the surface. Failure to clean the board properly can result in product failures and other issues.
Solution: Use a cleaning machine
To ensure proper cleaning of the board, it's important to use a cleaning machine. These machines are designed to remove all contaminants and debris from the surface of the board, leaving it clean and ready for use.
In conclusion, wave soldering is a popular and effective method of soldering through-hole components. However, as with any process, it can come with its own set of challenges. By using these solutions, we can overcome these challenges and ensure that our PCB assemblies are of the highest quality. So, when it comes to PCB assembly and wave soldering, be sure to follow these best practices and use a wave soldering machine to achieve optimal results.